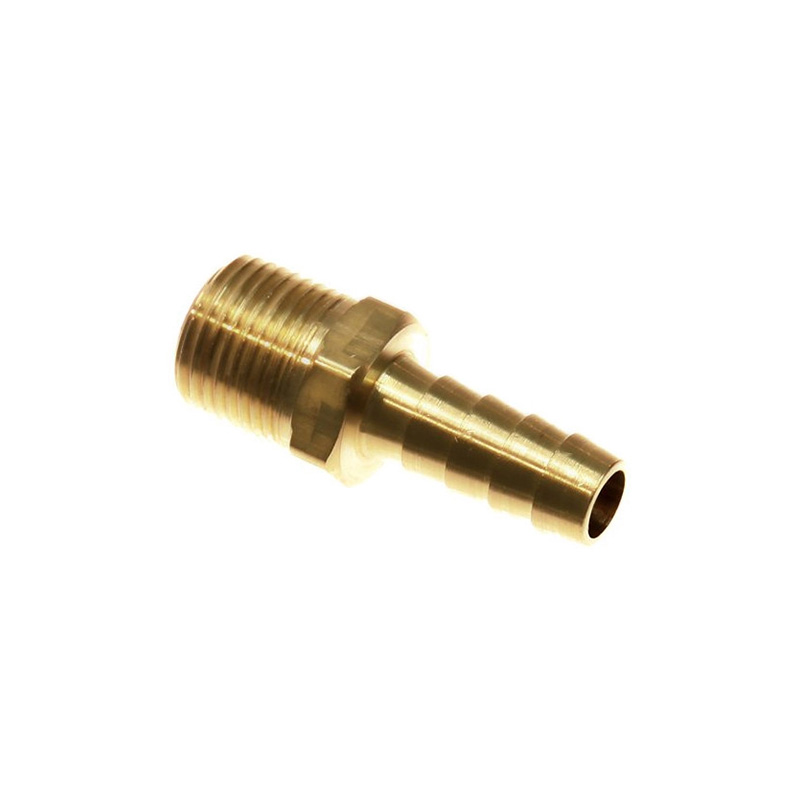
Manufacturers globally face relentless pressure to reduce production costs while maintaining precision. For CNC lathe parts—essential components in aerospace, automotive, and industrial machinery—this balance is particularly challenging. Surprisingly, up to 40% of machining expenses stem from avoidable design and process inefficiencies rather than material or labor costs. This guide reveals eight field-tested methods to optimize your production workflow, slash expenses, and maintain competitive pricing without compromising part quality.
Where Your Money Goes: The Hidden Cost Drivers
Understanding what impacts pricing is the first step toward smarter cost control. Six primary factors determine the final price of CNC lathe parts:
- Machining Time: Longer cycle times directly increase costs due to machine occupancy and labor :cite[1]
- Material Selection: Specialty alloys or hard metals (e.g., titanium) require slower cutting speeds and specialized tools, increasing costs by 50–70% compared to aluminum :cite[1]:cite[7]
- Tolerances: Tight tolerances (±0.01mm) demand additional setups, inspections, and increase scrap rates :cite[1]:cite[4]
- Quantity</strong》: Batch production spreads fixed setup costs across multiple units, reducing per-part expense :cite[1]
- Surface Finishes: Processes like anodizing or specialty coatings add post-processing time and cost :cite[1]:cite[5]
- Lead Time: Expedited orders incur 4–6% premiums due to production rescheduling :cite[1]
Smart Design: Optimize for Manufacturability
Over 60% of part costs are locked in during the design phase. These strategies ensure your CNC lathe parts are cost-effective to produce:
Avoid Over-Engineering
Specify tolerances only where critical. A ±0.05mm tolerance can be 30% cheaper to achieve than ±0.01mm while being sufficient for most applications :cite[1]:cite[4]. Similarly, skip cosmetic finishes like polishing or DLC coating unless functionally necessary.
Design for Tool Accessibility
Replace sharp 90° internal corners with radii (≥⅓ of cavity depth). This allows larger tools to machine continuously without repositioning, cutting cycle times by up to 15% :cite[1]. Fun fact: Our team redesigned a sensor housing in 2025 by increasing corner radii from 0.5mm to 1.5mm, reducing machining time by 22% without affecting performance.
Eliminate Thin Walls & Deep Pockets
Thin walls (<0.8mm for metal) cause vibration and tool deflection, requiring slower feeds and increasing scrap risk. Similarly, pockets deeper than 4x their width need specialized tooling or EDM processes. Aim for 2–3x depth-to-width ratios :cite[1].
Design Feature |
Standard Approach |
Cost-Optimized Approach |
Savings Impact |
Internal Corners |
90° sharp corners |
Radii ≥ tool diameter |
15–20% faster machining |
Thread Depth |
5x hole diameter |
3x hole diameter |
Reduces tap breakage risk |
Wall Thickness |
0.5mm (aluminum) |
≥0.8mm (aluminum) |
Lower scrap rate & vibration |
Material Matters: Choosing Cost-Effective Metals
Material costs and machinability significantly impact your budget for CNC lathe parts:
- Aluminum 6061: Ideal for most applications. Cuts 3x faster than steel, extends tool life, and costs less :cite[1]:cite[5]
- Brass C360: Excellent machinability and low tool wear. Perfect for fittings and connectors
- Avoid “Exotics”: Titanium or Inconel increases costs by 200–400% due to slow machining rates and tool wear :cite[7]
Pro Tip: Substitute SKH51 tool steel with SKD61 for mold pins—it performs similarly but costs 50–70% less :cite[1].
Production Strategies: Volume and Technology
Adjusting how you produce parts unlocks further savings:
Leverage Volume Discounts
Batch production amortizes setup and programming costs. Ordering 1,000 CNC lathe parts instead of 100 can reduce per-unit costs by 20–60% :cite[1]:cite[8].
Optimize Cutting Parameters
Contrary to intuition, maxing out spindle speed isn’t always efficient. A balanced approach works better:
- Maximize depth of cut to reduce passes
- Increase feed rate within surface finish limits
- Adjust speed to balance tool life and cycle time
For example, cutting aluminum at 500 SFM with a 0.012″ feed achieves optimal tool life and throughput :cite[7].
Warning: Avoid These Costly Missteps!
- Over-specifying Tolerances: ±0.01mm requires grinding or EDM vs. ±0.05mm achievable via standard turning
- Ignoring Standard Tool Sizes: Non-standard holes/threads need custom tools ($150–$500 per tool)
- Rushing Orders: Expedited fees add 10–25%; plan ahead for standard lead times
Supplier Collaboration: Build Partnerships
Your machine shop can be a valuable ally in cost reduction:
- Share Forecasts: Enable bulk material purchasing and production planning
- Standardize Finishes: Adopt their in-house capabilities (e.g., anodizing vs. PVD coating)
- Use Their Expertise: One client saved 31% by redesigning a part using the supplier’s tooling recommendations
For reliable, high-quality CNC lathe parts, partner with suppliers offering engineering support.
Cost-Saving Checklist for CNC Lathe Parts
Apply these steps before your next order:
- □ Replace sharp corners with radii ≥ tool diameter
- □ Specify tolerances > ±0.05mm unless critical
- □ Choose aluminum 6061 or brass C360 over steel/titanium
- □ Increase wall thickness to ≥0.8mm (metal) or ≥1.5mm (plastic)
- □ Limit threads to 3x hole depth
- □ Combine low-priority parts into batches
- □ Avoid expedited lead times (plan for 15–25 days)
- □ Request DFM feedback from your supplier
FAQs: CNC Lathe Parts Cost Reduction
What is the biggest cost driver for CNC lathe parts?
Machining time (45–60%) dominates costs, followed by material (30%) and setup (10–15%) :cite[1]:cite[7]. Optimizing design to reduce cycle time yields the highest ROI.
Can material choice reduce costs significantly?
Yes. Switching from stainless steel to aluminum cuts costs by 40–50% due to faster machining and lower material expense :cite[5].
Why avoid thin walls in turned parts?
Thin walls (<0.8mm) vibrate during machining, causing dimensional inaccuracy and higher scrap rates. Increasing thickness improves stability and reduces costs :cite[1].
How do tolerances impact pricing?
Tolerances tighter than ±0.05mm require special equipment, slower speeds, and additional inspections, increasing costs by 25–100% :cite[4].